Corrugated boxes come in a variety of styles and variables at Colony Packaging & Machine. Showing your packaging specialist the item you are packing, how it is shipping, and how it is being stored will give them a good roadmap to determine what style and strength you will need. Check out the following topics covering measuring the box, strength, style, material, and fluting.
Box Measurement
Measure a box using the inner dimensions of an assembled box – Length (L) x Width (W) x Depth (D). Looking at an assembled box, the longer of the two sides is considered the length, the shorter of the two sides is the width, and the side perpendicular to the length and width is the depth of the box.
The “Manufacturer’s Joint” is where the two ends of the side panels meet to form the box. At that point, the panels are fastened together with tape, staples (double or triple wall) or glue (single wall). This description applies to regular slotted shipping cartons (RSCs). The side panel thickness and content weight determine the type of seal used for the manufacturer’s joint.
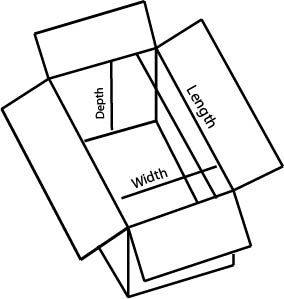
Strength
The strength of a corrugated box starts with its material. A corrugated sheet consists of two major components – linerboard and medium. Linerboard is the flat paper that covers both sides of the sheet and the medium is the “fluted” or arched paper found between both liners. The flute, when anchored to the linerboards with a starched based adhesive, resists bending and pressure from all directions. When placed vertically on its ends, the flutes form vertical columns, capable of supporting considerable amounts of weight.
Material
The amount of virgin pulp fibers and the length of those fibers in a corrugated sheet substantially contribute to box strength. For example, the difference between a 200# test box and a 275# test box is that the latter has more pulp fibers in its corrugated linerboard. The 200# test box is rated to hold up to 65 lbs. of box and contents while the 275# box can hold up to 95 lbs. A 350# test box is rated to hold up to 120 lbs. of box and contents. The following chart shows Bursting Test and Edge Crush Test performance standards of corrugated box liners based on the combined weight of a box and its contents.
Fluting
Flutes come in five basic heights and shapes – the most common are “B-Flute”(used for die-cut boxes) and “CFlute (used for RSCs). B-flute is compressed and appears thinner, but don’t be fooled. It is made with more paper to provide stronger side wall protection from blows and punctures. C-flute is taller, with more air space, but offers enhanced stacking strength. For excellent graphic reproduction, consider E-flute.
Popular Box Styles
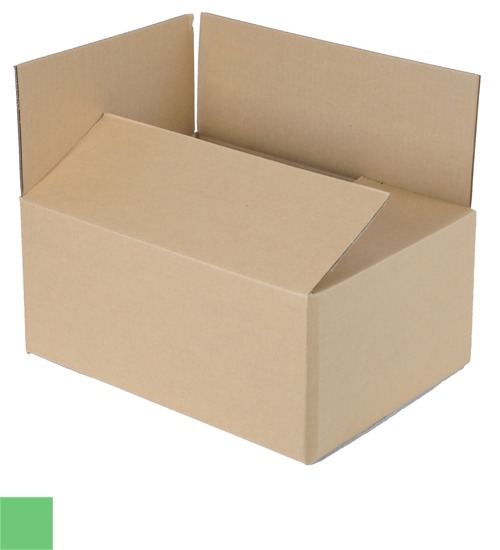
Regular Slotted Carton (RSC)

Full Telescope Design (FTD)
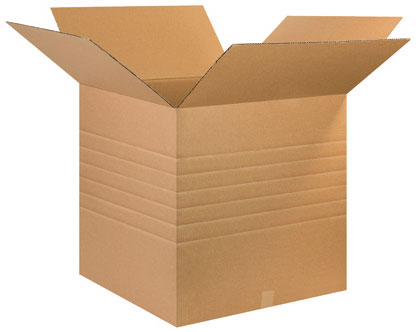
Multi-Depth Width (MDW)
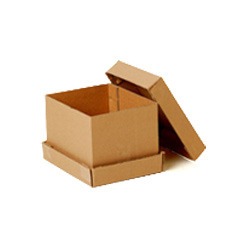
Double Cover Carton (DC)
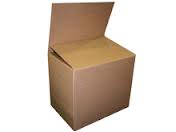
Full Overlap Slotted (FOL)
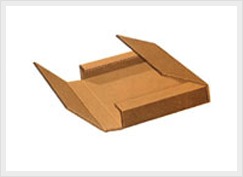
One Piece Folder (OPF)
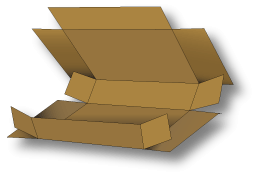
Five Panel Folder (FPF)
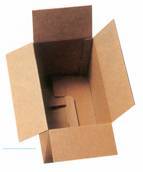
Snap Bottom Carton (SBC)
Wall Thickness
Singlewall Corrugated
This grade is used for lighter applications. Multiple light-weight objects work great for this box.
- one corrugated medium
- a total of three paper layers
Doublewall Corrugated
This grade is used for heavy applications, particularly in packaging for export and is excellent for stacking heavy items.
- two corrugated mediums
- an inner liner between the two mediums
- a total of five paper layers
Triplewall Corrugated
Looking for maximum strength? This is your board!
- total of seven paper layers
- used for very heavy industrial applications
- semi-bulk commodity bins, and many other uses
- excellent for stacking heavy items
Flute Size
Generally, larger flutes provide greater strength and cushioning, while smaller flutes have better printability and foldability. Flute profiles can be mixed and matched within the same piece of combined board, to manipulate printability, compression strengths, cushioning strengths and the total thickness of the board. For instance, CE double wall gets its durability from its C-flute layer, while the E-flute gives it a smoother printing surface.
-
A-Flute, the original flute, is the highest flute size, and therefore, when combined with an inner and outer facing, is the thickest. With 36 flutes to the foot, A-Flute makes the most of corrugated’s cushioning and stacking properties for fragile and delicate items. A-Flute offers excellent stiffness qualities and short column crush resistance.
The most common fluting companies will see is b-flute. It is what most RSC cartons are made of and the standard master carton in the industry. But, it is a great piece of information to know when considering printability, carton stacking, display and more.
Available Carton Sizes
The following is a snapshot of the thousands of carton sizes we offer for fast delivery. We offer stock cartons, custom sizes, and printed cartons. Looking to start a new carton program or get a cost competitive quote? Reach out directly to your Packaging Specialist or our Customer Care team to get started!